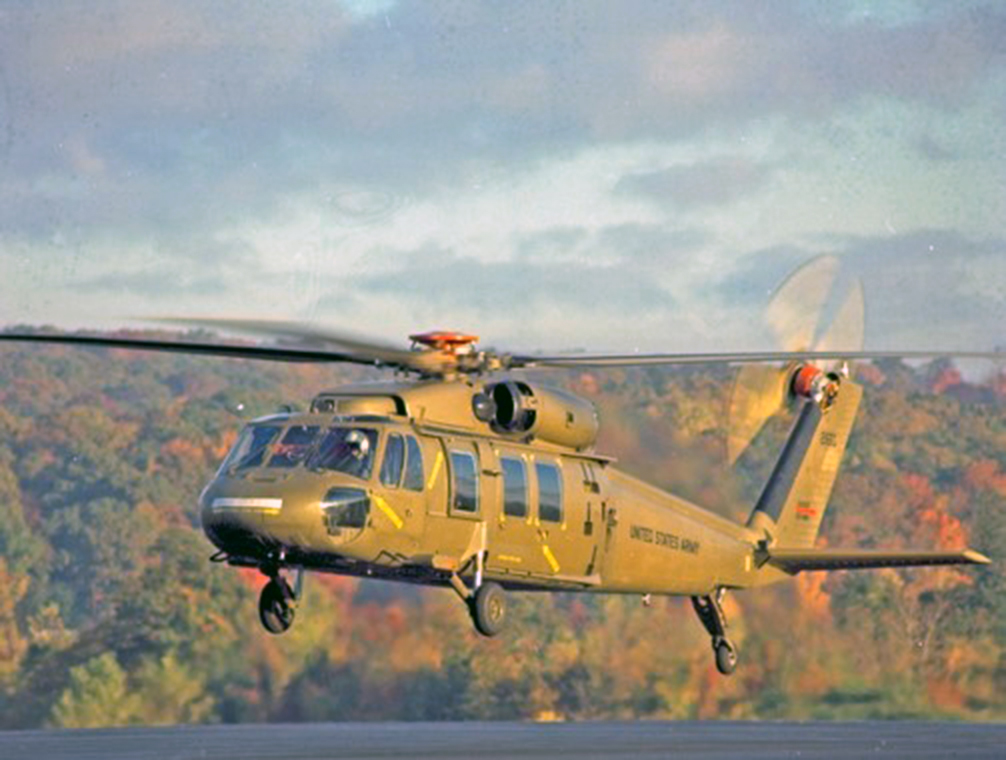
Early flight testing revealed excessive vertical vibrations associated with the main rotor. Extensive engineering and flight testing determined that this was caused by air flow upward through the rotor system and around the transmission and engine cowlings. The purpose of the low-mounted main rotor was to aid in fitting inside transport aircraft with minimal disassembly. It was necessary to increase the height of the mast and reshape the cowlings to achieve an acceptable level of vibration.
After eight months of testing, the U.S. Army selected the YUH-60A for production over its competitor, the Boeing Vertol YUH-61A. In keeping with the Army’s tradition of naming helicopters after Native Americans, the new helicopter was named Black Hawk, who was a 17th Century leader of the Sauk (or Sac) people.
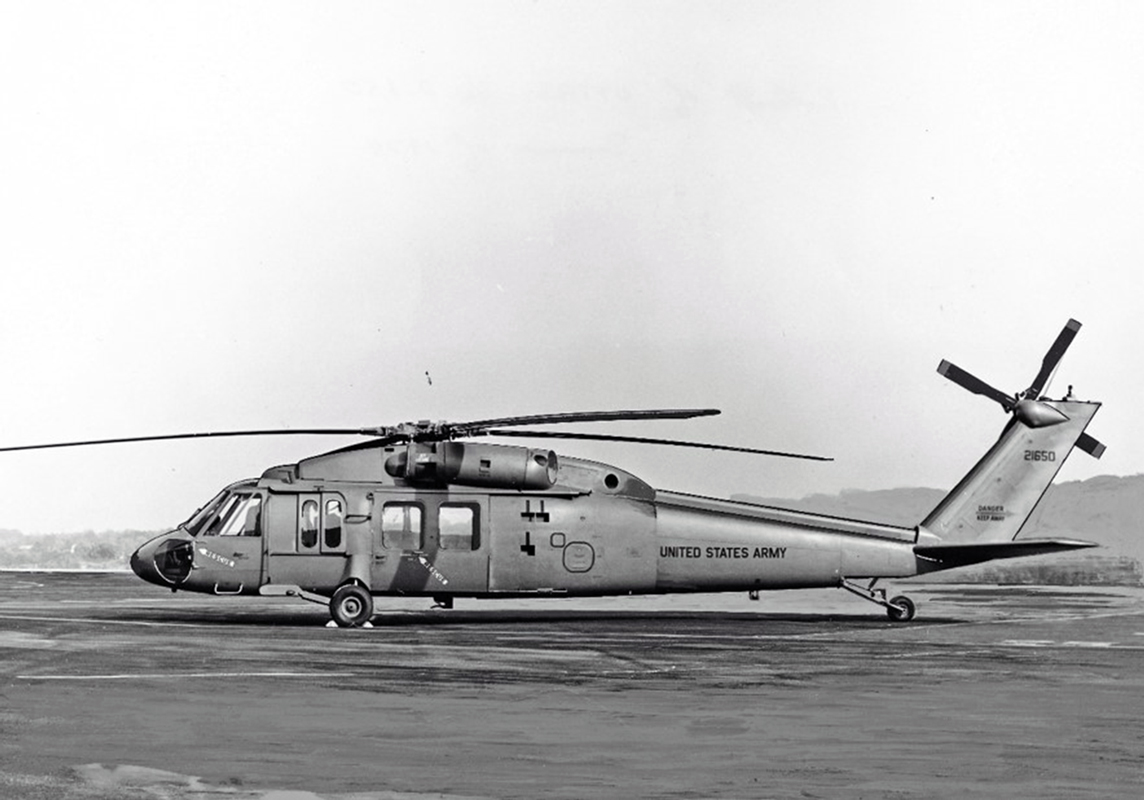
The Sikorsky Model S-70 (YUH-60A) was designed to meet the requirements of the U.S. Army Utility Tactical Transport Aircraft System (UTTAS). It had a 3-man crew and could carry an 11-man rifle squad. The helicopter could be transported by a Lockheed C-130 Hercules.
The three UTTAS prototypes were 63 feet, 6 inches (19.355 meters) long, with rotors turning. The span of the horizontal stabilizer was 15 feet, 0 inches (4.572 meters). The prototypes’ overall height was 16 feet, 10 inches (5.131 meters).
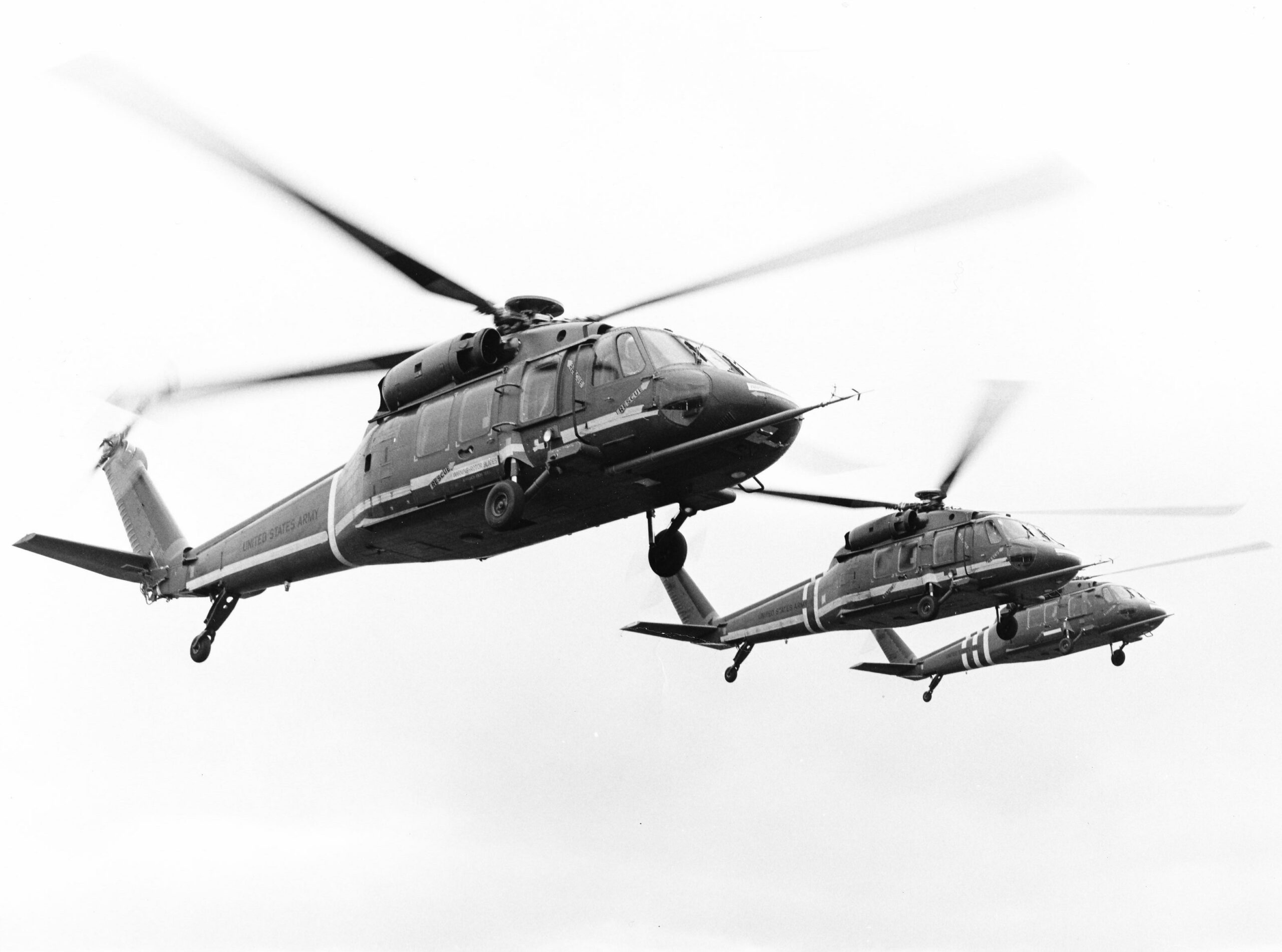
The YUH-60A had an empty weight of 11,182 pounds (5,072 kilograms) and gross weight of 16,750 pounds (7,598 kilograms). The helicopter had a structural load factor of 3.5 Gs. With 1,829 pounds (830 kilograms) of fuel, it had an endurance of 2 hours, 18 minutes.
The YUH-60A had a four-blade fully-articulated main rotor with elastomeric bearings. It had a diameter of 52 feet, 0 inches (15.850 meters). During flight testing, the diameter was increased to 52 feet, 4 inches (15.951 meters), and finally to 52 feet, 8 inches (16.053 meters). The blades were built with titanium spars and used two different airfoils and a non-linear twist (resulting in a net -16.4°). The outer 20 inches (0.508 meters) were swept aft 20°. These characteristics improved the helicopter’s maximum speed and hover performance. The main rotor turned counterclockwise, as seen from above (the advancing blade is on the right) at 258 r.p.m. The blade tip speed was 728 feet per second (222 meters per second). During flight testing it was decided to change the main transmission gear reduction ratio in order to operate the engines at a slightly increased r.p.m. At the higher r.p.m., the engines produced an additional 50 horsepower, each.
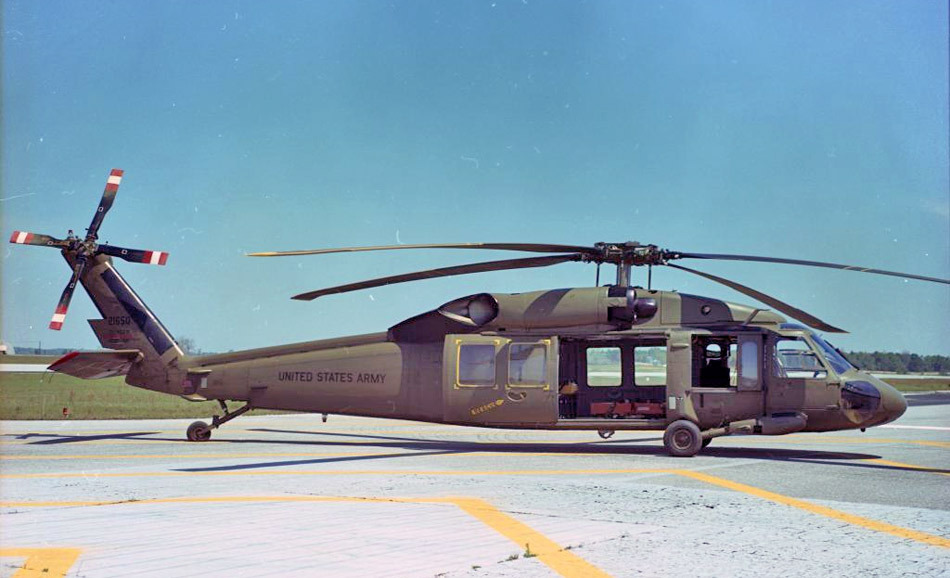
The four-bladed bearingless tail rotor was positioned on the right side of the tail rotor pylon in a tractor configuration. The tail rotor diameter was 11 feet (3.353 meters), and turned 1,214 r.p.m., rotating clockwise as seen from the helicopter’s left (the advancing was blade below the axis of rotation). The blade tip speed was 699 feet per second (213 meters per second). The tail rotor blades had -18° of twist. Because the Black Hawk’s engines are behind the transmission, the aircraft’s center of gravity (c.g.) is also aft. The tail rotor plane is inclined 20° to the left to provide approximately 400 pounds of lift (1.78 kilonewtons) to offset the rearward c.g.
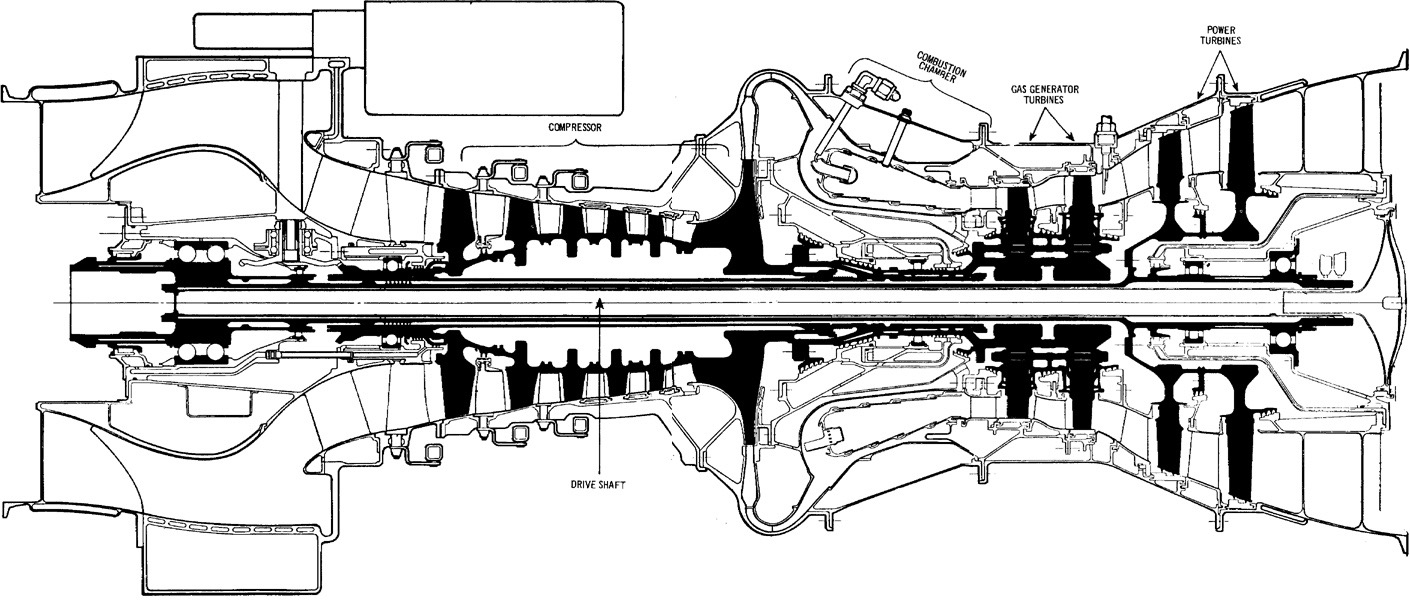
The YUH-60A had a cruise speed of 147 knots (169 miles per hour/272 kilometers per hour) at 4,000 feet (1,219 meters) and 95 °F. (35 °C.). It could climb at 450 feet per minute (2.29 meters per second) at the same altitude and air temperature.
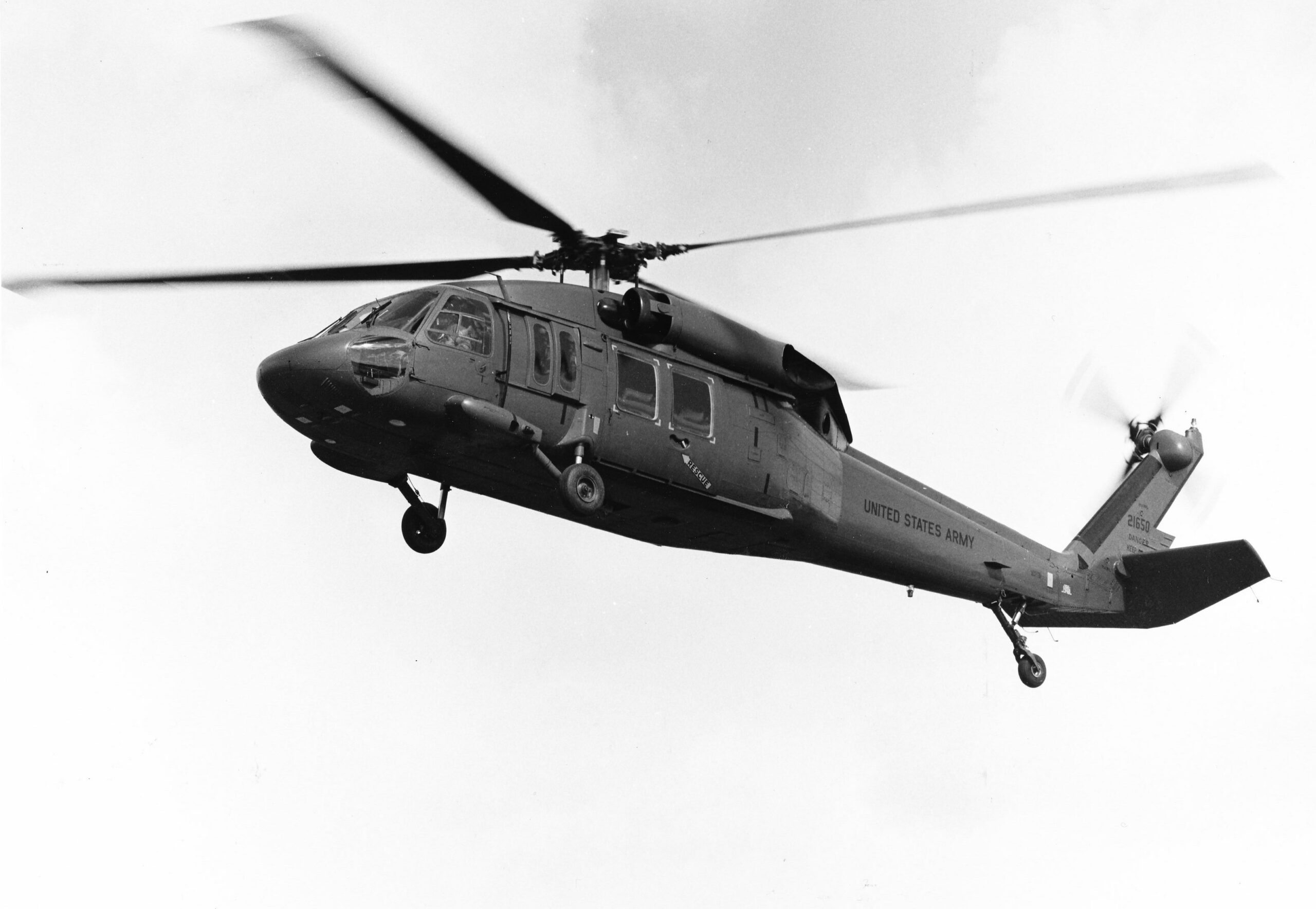
While operating with an Army crew on the night of 9 August 1976, YUH-60A 73-21650 developed a significant vibration. An emergency landing was made. Because of darkness and mist, the pilots thought they were landing in a corn field, but it was actually a pine tree plantation. The helicopter’s rotors cut down more than 40 trees with trunk diameters up to 5 inches (12.7 centimeters).
Close inspection by Army and Sikorsky personnel found that the only visible damage was to the four main and four tail-rotor blades other than nicks and dents to the airframe that were of no structural concern. All gearboxes and engines turned freely, and all flight controls responded properly. ¹ The blades were replaced on-site and the helicopter was flown out the following day.
73-21650 crashed into the Housatonic River near the Stratford plant at 9:10 a.m., Friday, 19 May 1978, killing all three Sikorsky employees on board, pilots Albert M. King, Jr., John J. Pasquarello, and flight engineer John Marshall.
During routine maintenance an airspeed sensor for the all-flying tailplane had been disconnected. As the Black Hawk transitioned from hover to forward flight, the all-flying tailplane remained in the hover position and forced the helicopter’s nose to pitch down to the point that recovery was impossible.
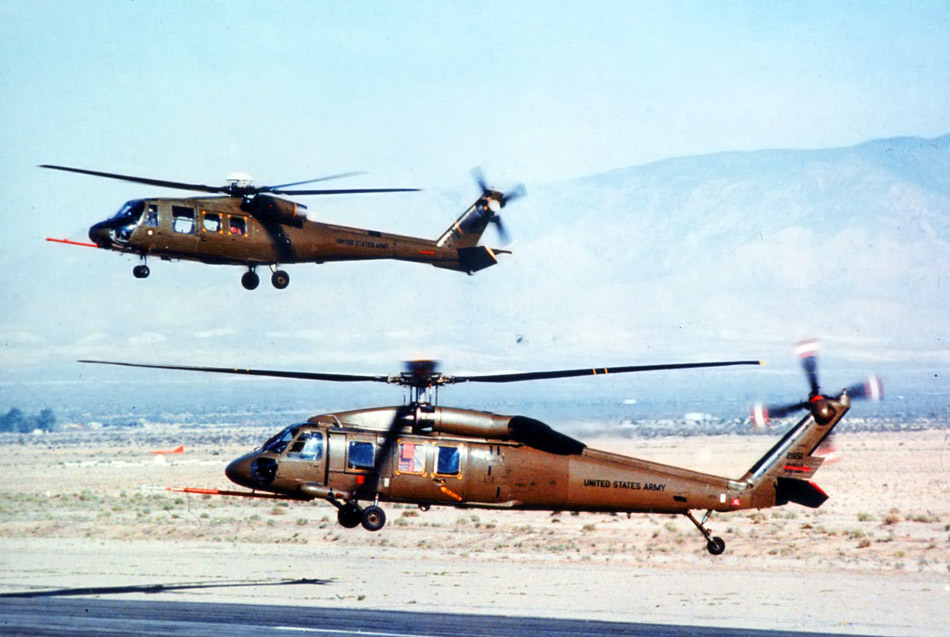
The Black Hawk has been in production since 1978. More than 4,000 of the helicopters have been built and the type has been continuously improved. The current production model is the UH-60M.
Sikorsky is a Lockheed Martin Company.
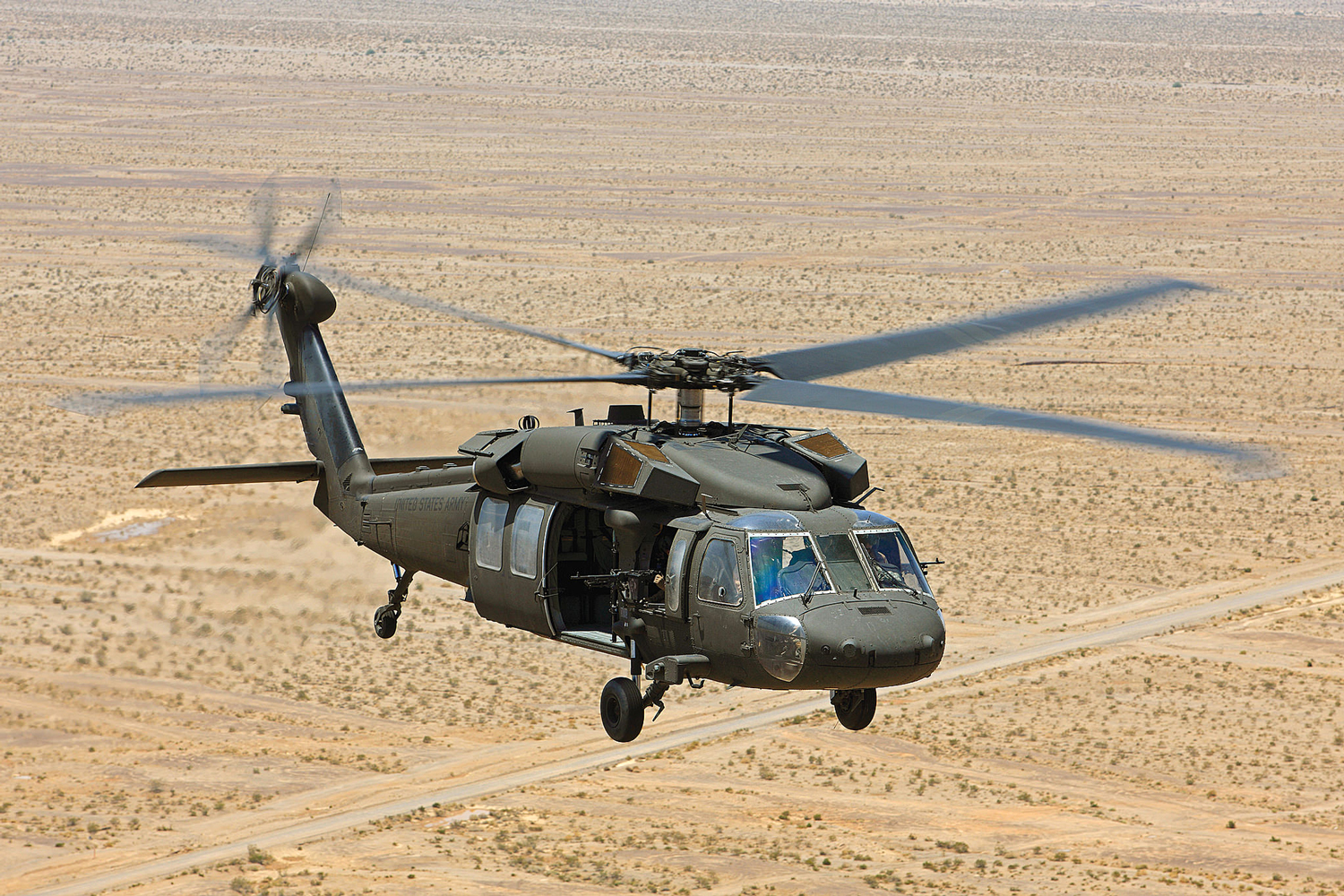
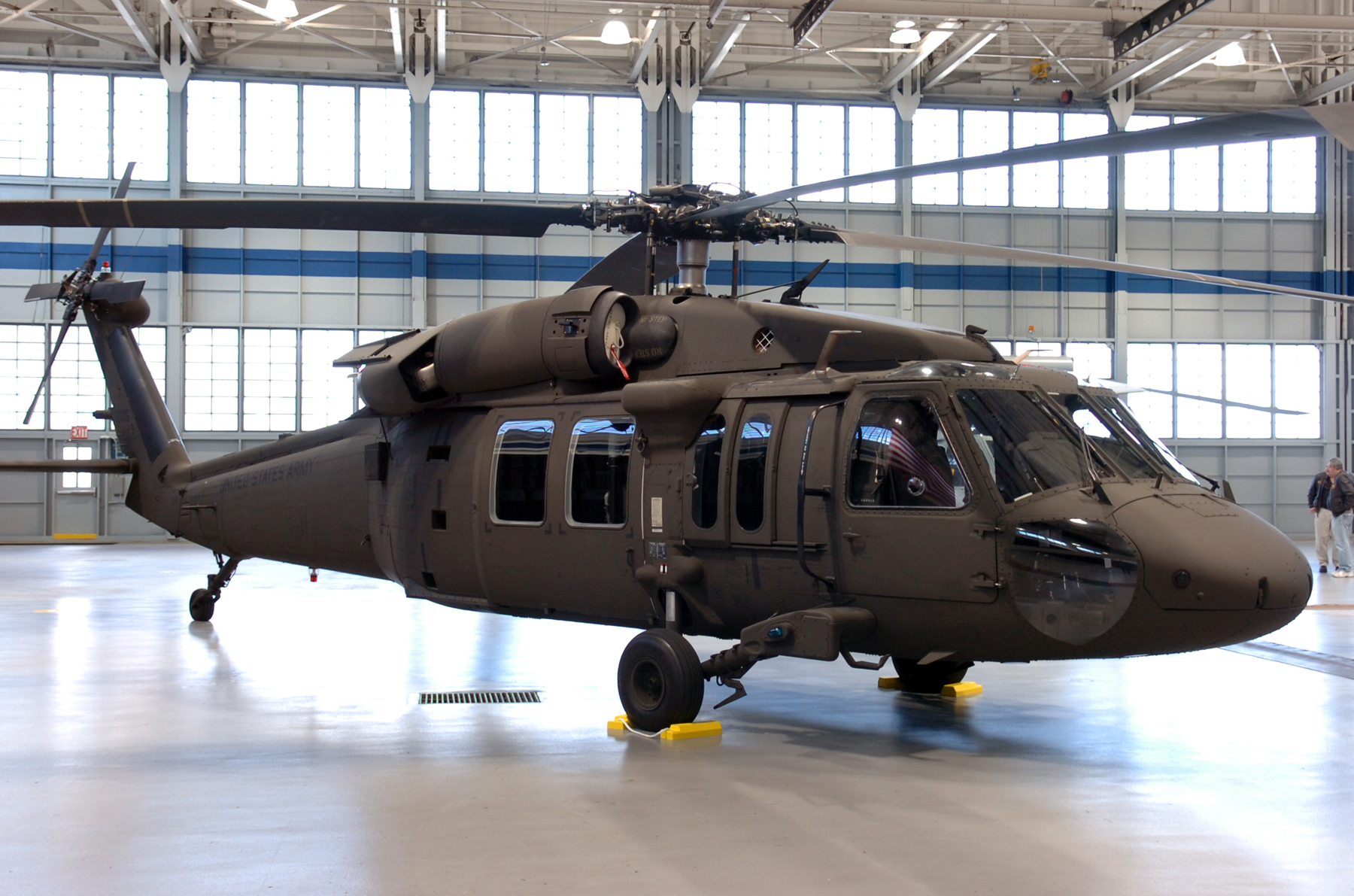
¹ Black Hawk: The Story of a World Class Helicopter, by Ray D. Leoni, American Institute of Aeronautics and Astronautics, Reston, Virginia, 2007, Chapter 8 at Page 173.
© 2019, Bryan R. Swopes
It seems strange that the accident you mention with this tail number occurred to other UH-60’s before the Army modified them all a decade later. The UH-60 was grounded and at one point, in ’87, limited to 80kts because of issues with the ‘stabilator’.
I believe those cases were due to a shielding issue on the stab system. The case mentioned in the sorry was due to a cannon plug not connected after maintenance was performed.
Totally enjoyed maintaining this machine for my first 15 years of my 25. I was assigned to the 82nd Abn, 82nd CAB when we first received ours in mid 1980s. Fabulous improvement over the UH-1 Huey. Unfortunately, we also suffered a number of class A & B accidents. I was a Crew Chief not a pilot at the time and in my opinion the amount of power and performance would catch pilots off guard. Contribute that with minimum training requirements at Mother Rucker at the time. Over the years the aircraft
Upgrades and modifications have dramatically improved its overall performance and reliability.
Fly Safe All,
Love the Blackhawk 👍
As I’m not familiar, would someone kindly explain the aerodynamics of the ‘tail plane’? (Sync elevator as I know it).
Why was it designed this way? I’m a Bell Helicopter guy and always wondered why Sikorsky designed it this way.
Thanks in advance.
Chris, the variable incidence stabilizer (“stabilator”) controls aircraft pitch in horizontal flight, improving handling characteristics and increasing airspeed. In a hover or low-speed flight, it minimizes downwash effects by reducing nose-up attitudes during transition to hover and improves pilot visibility during low speed flight. It moves through a range of +40° to -8°. It is a fly-by-wire system with no direct pilot input. The three prototypes were built with fixed stabilizers, but were retrofitted as the stabilator was developed.
Sorry this has nothing to do with this article but the one I just saw was closed for comments.. if you like I will look around for my picture of the flight of the first flying wing at Pearson airfield Vancouver WA it was before 1920 I believe my great uncle Irvin Joy Invented it and my grandfather Marvin England helped him build it and started the engines to fly it everyone at the airfield said he was crazy it couldn’t fly without a fueslage or tail it had two engines on the back of the wing pushing it my mother has a broken proeller from it my grandfather carved those well to the surprise of everyone at the airport the wing flew the rudders mounted on the engines did not work it flew 1500 feet leaned to one side steeply and crashed. My grandma told my the army showed up and took the wing from her brother took it to fort Lewis in Washington and told Irvin and my grandfather not to talk about it to anyone it was to be hidden for national security and no one saw it again untill Northrup built an identical one out of metal the original one was wood and cloth . I have a photograph with a good description of the plane a copy of the photo at Pearson air museum in Vancouver it’s of the plane warming up one engine and my grandfather starting the other right before it flew.