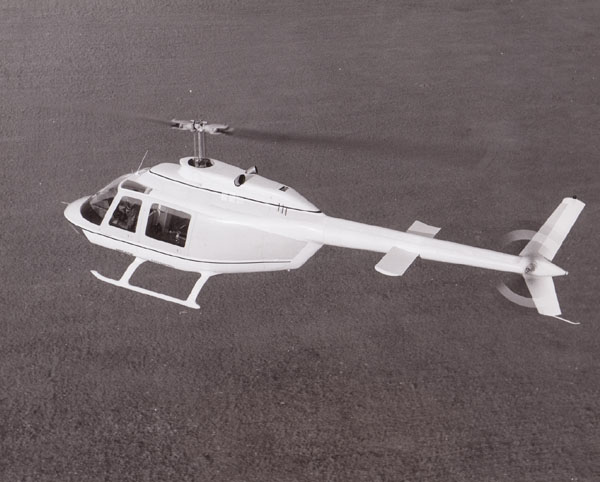
10 January 1966: The prototype Bell Model 206A JetRanger serial number 1, N8560F, made its first flight at at the Bell Helicopter Company plant at Hurst, Texas. This aircraft would be in production for almost 45 years. The final JetRanger to be built, Bell 206B-3 serial number 4690, was delivered in December 2010 and production came to an end.
During early production of the Model 206A, cabin sections were built by Beechcraft and Agusta then shipped to Bell at Fort Worth. (The vertical seam just to the rear of the fuel cap distinguished the two.) Oil pressure and temperature gauges for the engine and transmission, the loadmeter and fuel quantity indicator were provided by Cessna.
The Bell JetRanger is a 5-place, single-engine light civil helicopter based on the Bell Helicopter’s unsuccessful OH-4 entrant for the U.S. Army’s Light Observation Helicopter (LOH, or “loach”) contract. It is flown by a single pilot in the right front seat. Dual flight controls can be installed for a second pilot. The helicopter was certified for VFR flight, but could be modified for instrument flight.
The industrial design firm of Charles Wilfred Butler
“. . . was responsible for the complete redesign of the Bell OH-4A prototype army helicopter (1961) into the Bell Jet Ranger (1965). He and his designers restyled the machine inside and out in the manner of automotive design, creating in the process one of the world’s most successful and beautiful helicopters.”
—Encyclopedia Britannica.
The JetRanger is 38 feet, 9.5 inches (11.824 meters) long, overall. On standard skid landing gear the overall height is 9 feet, 4 inches (2.845 meters). The Bell 206A has an empty weight of approximately 1,700 pounds (771 kilograms), depending on installed equipment. The maximum gross weight is 3,200 pounds (1,451.5 kilograms). With an external load suspended from the cargo hook, the maximum gross weight is increased to 3,350 pounds (1,519.5 kilograms).
The two-bladed main rotor is semi-rigid and under-slung, a common feature of Bell’s main rotor design. It has a diameter of 33 feet, 4.0 inches (10.160 meters) and turns counter-clockwise (seen from above) at 394 r.p.m. (100% NR). (The advancing blade is on the helicopter’s right side.) The rotor blade has a chord of 1 foot, 1.0 inches (0.330 meter) and 10° negative twist. The airfoil is symmetrical. The cyclic and collective pitch controls are hydraulically-boosted.
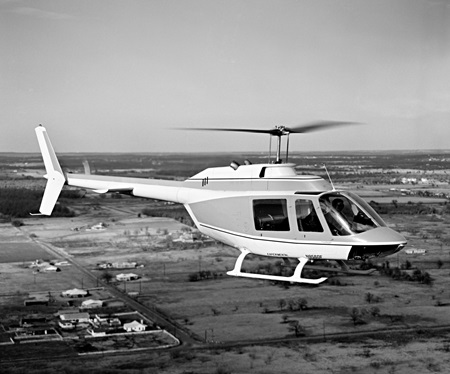
The two-bladed tail rotor assembly is also semi-rigid and is positioned on the left side of the tail boom in a pusher configuration. It turns at 2,550 r.p.m., clockwise, as seen from the helicopter’s left. (The advancing blade is below the axis of rotation.) The tail rotor diameter is 5 feet, 6.0 inches (1.676 meters).
The turboshaft engine is mounted above the roof of the fuselage, to the rear of the main transmission. Output shafts lead forward to the transmission and aft to the tail rotor 90° gear box. The transmission and rotor mast are mounted tilting slightly forward and to the left. This assists in the helicopter’s lift off to a hover, helps to offset its translating tendency, and keeps the passenger cabin in a near-level attitude during cruise flight.
A vertical fin is attached at the aft end of the tail boom. The fin is offset 4° to the right to unload the tail rotor in cruise flight. Fixed horizontal stabilizers with an inverted asymmetric airfoil are attached to the tail boom. In cruise flight, these provide a downward force that keeps the passenger cabin in a near-level attitude.
The 206A was powered by an Allison 250-C18 turboshaft engine (T63-A-700) which produced a maximum of 317 shaft horsepower at 104% N1, 53,164 r.pm. The improved Model 206B JetRanger and 206B-2 JetRanger II used a 370 horsepower 250–C20 engine, and the Model 206B-3 JetRanger III had 250-C20B, -C20J or -C20R engines installed, rated at 420 shaft horsepower at 105% N1, (53,519 r.p.m.). Many 206As were upgraded to 206Bs and they are sometimes referred to as a “206A/B.” The Allison 250-C20B has a 7-stage compressor section with 6-stage axial-flow stages, and 1 centrifugal-flow stage. The 4-stage axial-flow turbine has a 2-stage gas producer (N1) and 2-stage power turbine (N2). These were very light weight engines, ranging from just 141 to 173 pounds (64.0 to 78.5 kilograms).
The helicopter’s main transmission is limited to a maximum input of 317 shaft horsepower (100% Torque, 5-minute limit). The engine’s accessory gear unit reduces the output shaft speed to 6,016 r.p.m. N2, which is further reduced by the transmission’s planetary gears, and the tail rotor 90° gear box.
The JetRanger has a maximum speed, VNE, of 150 miles per hour (241 kilometers per hour) up to 3,000 feet (914 meters). Its best rate of climb, VY, is at 60 miles per hour (97 kilometers per hour) and best speed in autorotation (minimum rate of descent and maximum distance) is at 80 miles per hour (129 kilometers per hour), resulting in a glide ratio of about 4:1. The service ceiling is 13,500 feet (4,145 meters) with the helicopter’s gross weight above 3,000 pounds (1,361 kilograms), and 20,000 feet (6,096 meters) when below 3,000 pounds. The helicopter has a maximum range of 430 miles (692 kilometers).
After being used as a factory demonstrator and development aircraft, N8560F was retired from flight status and used as a maintenance ground training device at Bell’s training school at Hurst.
Note: The Model 206A-1 was adopted by the U.S. Army as the OH-58A Kiowa. Though very similar in appearance to the Model 206A and 206B, the OH-58A differs significantly. Few of the parts are interchangeable between the types.
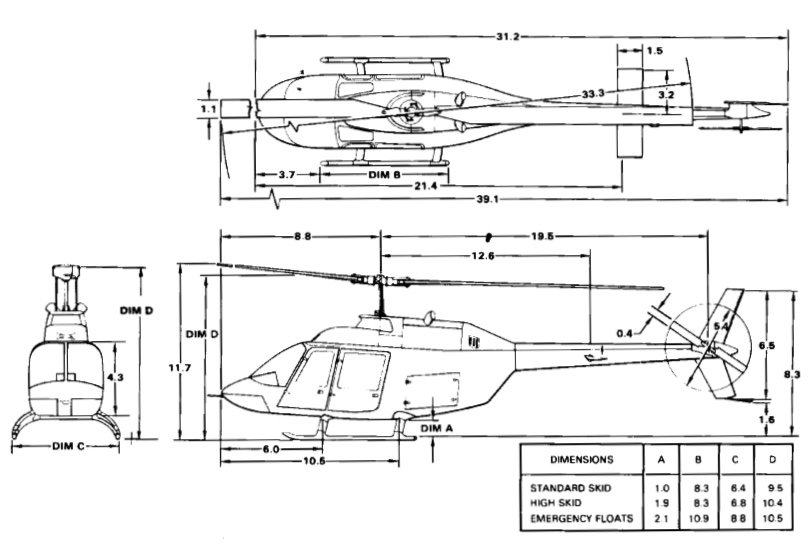
© 2018, Bryan R. Swopes